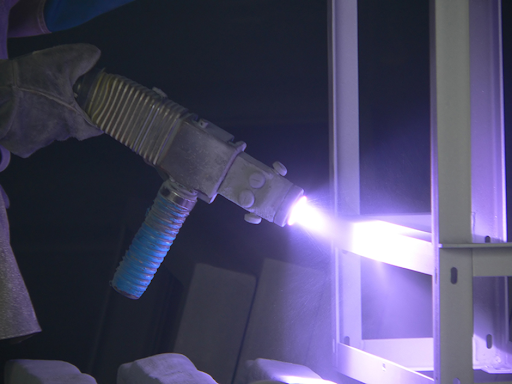
Different Methods of Galvanization
Galvanization is essential for enhancing the durability of steel and iron by applying a
protective coating to prevent rust. Each method of galvanization offers unique benefits and
applications, allowing manufacturers to choose the best option for their needs. Here, we
discuss the most common galvanization methods and their advantages.
1. Hot Dipped Galvanization
Hot-dipped galvanization involves immersing steel or iron in molten zinc, forming a robust,
long-lasting coating that shields against rust and corrosion. Widely used across industries,
this method provides strong protection, particularly in outdoor environments.
Advantages:
- Durable Protection: Offers a strong, lasting barrier against corrosion.
- Cost-Effective: Suitable for large-scale production at a low cost.
- Versatile: Commonly used on items like fences, bridges, and roofs.
Drawbacks:
- Environmental Considerations: Requires careful handling due to potential environmental impact.
2. Electroplating (Cold Dip Galvanization)
Electroplating involves placing the metal in an electrolyte solution and applying an electric
current, which deposits a thin zinc layer. Often used for decorative purposes, this method also
provides moderate corrosion protection.
Advantages:
- Thin Coating: Protects without adding much bulk, ideal for items needing a sleek finish.
Drawbacks:
- Less Durable: The thinner coating may not be as resilient as hot-dipped galvanization.
3. Sherardizing (Vapor or Dry Galvanization)
Sherardizing involves heating metal with zinc dust in a rotating drum, creating a zinc-iron
alloy layer that adheres well and resists corrosion. Named after its inventor, Sherard Osborn
Cowper-Coles, this method is particularly effective for small or complex parts.
Advantages:
- Corrosion Resistance: Provides a durable and adhesive coating.
- Geometry Maintenance: Retains the metal’s original shape.
- Prevents Hydrogen Embrittlement: The hydrogen-free process avoids brittleness.
Drawbacks:
- Less Durable: The thinner coating may not be as resilient as hot-dipped galvanization.
4. Thermal Spraying
In thermal spraying, melted zinc or zinc alloys are sprayed onto a prepared metal surface.
This process forms a coating that offers both barrier and galvanic protection, making it highly
effective in challenging environments.
Process:
- The surface is prepared through grit blasting to enhance bond strength.
- Zinc is melted using an electric arc or combustion flame and sprayed to create a thick protective coating.
Application:
- Ideal for marine and harsh atmospheric environments where thick, robust protection is required.
Advantages:
- Customizable Thickness: Thickness ranges from 50–500 microns, allowing for application in highly corrosive conditions.
- Efficient Edge Coating: Ensures even coating on edges, commonly difficult for other methods.
Conclusion
There are several different methods of galvanization, each with its own advantages and
disadvantages. The best method for your project will depend on the specific needs of the
project. Whichever method you choose, galvanization is an effective way to prevent
corrosion and extend the life of your metal products.
By understanding these galvanization options, businesses can make informed decisions to
enhance the longevity and durability of their products. At Sunshine Wire Industries, we offer
high-quality electro-galvanized solutions to meet diverse industry needs.
Contact us at sunshinewire164@gmail.com or call us at +91 9967703366. At Sunshine
Wire Industries, we believe in client satisfaction
The Essential Role of Stitching Wire in Packaging Corrugated and Carton Boxes
- September 20, 2024